El concepto “Just in time”, conocido con las siglas JIT, es un sistema de gestión empresarial desarrollado por la automotriz japonesa Toyota, basado en optimizar los métodos productivos y orientarlos a la demanda. El objetivo es satisfacer al cliente en el momento que lo desea, en la cantidad que desea y con productos de alta calidad a precios competitivos.
Dentro del Sistema de Producción de Toyota, el JIT es uno de los dos pilares (junto con Jidoka) que sustenta toda la metodología que ha revolucionado los conceptos de abordar la producción en función de la demanda; y sobre la que en occidente se ha basado el concepto de “Lean Manufacturing”.
- Inicie sesión para enviar comentarios

Si bien suele interpretarse que este último es la adaptación occidental del TPS, debe considerarse como diferencia fundamental que TPS es mucho más que una serie de herramientas o técnicas aplicadas durante el proceso de producción.
TPS “es un Sistema” que surge de la necesidad de adaptar la industrialización a las necesidades de los consumidores, contemplando factores tales como suministrar la máxima calidad al menor costo; a la vez que sitúa al operario que ejecuta los procesos como el centro de los mismos y factor fundamental para el éxito.
Conceptualmente el JIT se basa en 7 pilares fundamentales:
- Igualar la oferta y la demanda. No importa lo que pida el cliente, hay que producirlo como se requiera y cuando se requiera. Hay que buscar que el tiempo de entrega (Lead Time) se reduzca al mínimo, esto se consigue por ejemplo, reduciendo los tiempos de cambio, las esperas y los tamaños de lotes.
- El peor enemigo es el desperdicio. Se debe constantemente eliminar las causas raíz que generan desperdicios (solo agregan costo sin agregar valor) en todos los procesos principales y auxiliares.
- El proceso debe ser continuo no por lotes. Esto significa que se deben producir solo las unidades necesarias en las cantidades necesarias, en el tiempo mínimo necesario. Para lograrlo se debe considerar:
- Tener los tiempos de entrega muy cortos. Es decir, que la velocidad de producción sea igual a la velocidad de consumo y que se tenga flexibilidad en la línea de producción para cambiar de un modelo a otro rápidamente.
- Eliminar los inventarios innecesarios. Para eliminar los inventarios se requiere reducirlos poco a poco. El inventario oculta los problemas existentes generando una falsa sensación de que “todo está bien, hemos cumplido” y por ende no es necesario mejorar nada…
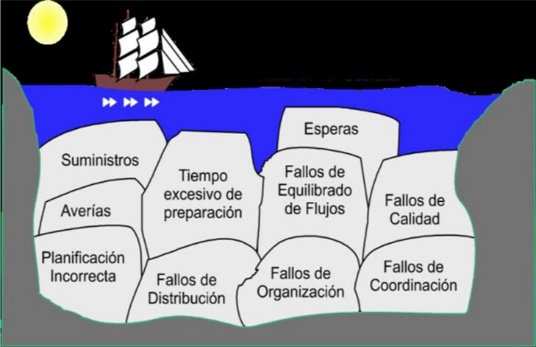
- Mejora Continua. La búsqueda de la mejora debe ser constante, tenaz y perseverante paso a paso para así lograr las metas propuestas.
- Primero el ser humano. La gente es el activo más importante. Se considera que el hombre es la persona que está con los equipos, y ejecuta los procesos; por lo que son claves sus decisiones y estas logran llevar a cabo los objetivos de la empresa.
- La sobreproducción es sinónimo de ineficiencia. Se debe eliminar el “por si acaso” utilizando otros principios como son la Calidad Total, organización del lugar de trabajo, Mantenimiento Productivo Total (TPM), Cambio rápido de modelo (SMED), Flujo Continuo de Proceso (OPF), simplificar comunicaciones, etc.
- No vender el futuro. Las metas actuales tienden a ser a corto plazo, hay que reevaluar los sistemas de medición, de desempeño, etc. El JIT no solo implica al proceso productivo, para planificar también hay que usar esta filosofía dado que como ya hemos dicho debemos ver la empresa como un sistema.
Conceptos integrales del Sistema JIT
Ya hemos mencionado que JIT es parte de un sistema, una forma definida de hacer las cosas. No puede decirse que hemos desarrollado una gestión JIT si no hemos incorporado todas las herramientas o metodologías que dan estructura a este pilar y son, entre otras:
- Eliminación constante de los desperdicios. (MUDA en japonés) que agregan costo a los procesos, “estiran” los tiempos de ciclo, son en muchas ocasiones causales de accidentes y/o degradan los resultados de calidad.
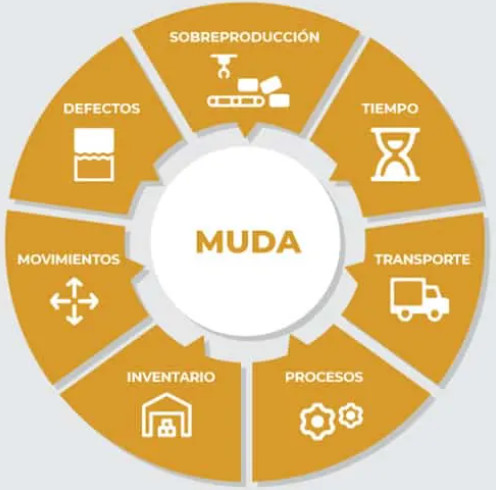
Este proceso de mejora permanente se ejecuta mediante la metodología KAIZEN (suele ejecutarse bajo el estándar del ciclo PDCA y/o metodología Problem Solving) y los trabajadores son los protagonistas principales en esta gestión dado que “Nadie conoce mejor el trabajo que aquél que lo ejecuta a diario”.
También es necesario identificar y eliminar MURA (desbalanceo) y MURI (sobrecarga).
- Sistema de Producción Pull. Consiste en “Jalar” el Producto a través del Proceso de Manufactura al ritmo de la demanda del cliente “NO MÁS - NO MENOS”. Para implementar esta metodología, suele emplearse la herramienta Kanban.
- Kanban. Es un sistema para manejar los flujos de material e información de manera sencilla y visual. El significado de esta palabra en japonés es “tarjeta”. Existen y se implementan, conforme a las necesidades del proceso, distintos sistemas de Kanban; por ejemplo, Kanban de retiro, Kanban de producción, Kanban de señal, etc.
- Takt Time. Es un tiempo calculado. Determina cuál debe ser la velocidad de producción. En otras palabras, el TAKT TIME determina el ritmo de producción para abastecer las necesidades de la demanda a tiempo sin que se generen inventarios innecesarios.
- Value Stream Map (VSM). Conocida también como Mapeo de la Cadena de Valor, esta herramienta permite identificar cuellos de botella, demoras, acumulaciones de inventarios, tiempos muertos que no agregan valor dentro del proceso y solo retrasan la capacidad de respuesta ante la demanda. Cabe destacar la importancia de analizar y mejorar tanto el flujo de materiales, como así también el flujo de la información.
- Single Minute Exchange of Dies (SMED). También conocida como cambio rápido de herramientas y/o utillaje, esta técnica permite minimizar los tiempos de máquina parada ante la necesidad de cambios de modelo. El minimizar el tiempo de máquina parada ante un cambio de modelo, dará a la organización la suficiente flexibilidad para atender las necesidades de la demanda sin la necesidad de generar inventarios.
- Mantenimiento Productivo Total (TPM). La implementación de esta técnica dentro del sistema, permitirá la disponibilidad siempre del equipamiento necesario para la operación (máquinas, infraestructura, etc.) en condiciones óptimas de uso a efectos de lograr los resultados esperados sin costos extras.
Vale también aclarar que es fundamental para la implementación del sistema JIT que el pilar JIDOKA se encuentre también implementado dado que se prevé que todo lo fabricado cumple con los estándares de calidad definidos. Aunque parezca reiterativo la efectividad del TPS radica en la implementación de todos sus componentes como un Sistema.